水泥的配方揭秘:从原材料到添加剂的全面解析
水泥是我们日常生活中无处不在的建筑材料,但你有没有想过它到底是怎么“炼”出来的?其实,水泥并不是一种天然存在的物质,而是通过科学配比和高温煅烧等多种工艺制造而成。而其中最关键的一环,就是它的配方。水泥的配方就像是一道菜谱,原材料的选择、比例的调配,都会直接影响最终产品的性能和质量。
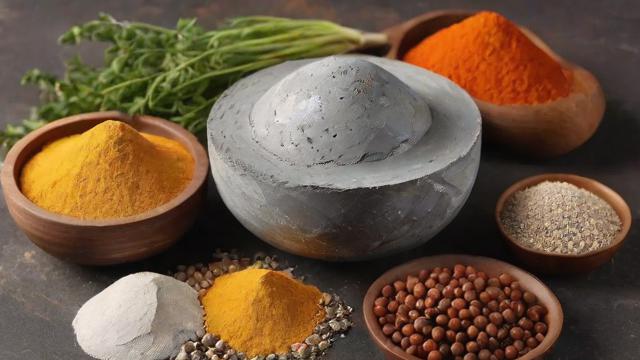
在水泥生产中,配方设计不仅仅是简单的材料混合,它背后有着严谨的化学和物理原理支撑。了解水泥配方的基本构成,有助于我们更好地理解不同类型水泥的用途以及它们为何适用于特定的工程环境。接下来的内容里,我会从原材料讲起,带你看清水泥是如何一步步成型的。
主要原材料及其作用
水泥的原材料虽然看起来很普通,但每一样都扮演着不可或缺的角色。最常见的三种原料是石灰石、黏土和铁矿石。石灰石主要提供氧化钙(CaO),这是形成硅酸盐矿物的核心成分;黏土则富含二氧化硅(SiO₂)和氧化铝(Al₂O₃),它们在高温下与氧化钙发生反应,生成具有胶凝性能的化合物;铁矿石的作用相对辅助,但它能调节熟料中的液相组成,帮助物料在窑内更好地熔融和反应。
这些原材料在进入生产线之前,都要经过严格的筛选和配比计算。比如,如果石灰石含量过高,会导致水泥的安定性变差;而黏土太少,则会影响水泥的强度发展。因此,在实际操作中,工程师们会根据目标水泥的性能需求,调整这几种原料的比例,确保最终产品既稳定又高效。
我自己第一次走进水泥厂时,看到那些灰白色的粉末状原料堆在一起,完全想不到它们会在高温窑炉中发生如此神奇的化学变化。正是这些看似普通的材料,经过精确控制的配比和加工,才形成了我们今天所熟知的水泥。
不同类型水泥的配方差异
虽然大多数水泥的基础原料相似,但不同类型的水泥在配方上还是存在明显差异。以最常用的硅酸盐水泥为例,它的熟料含量较高,通常在75%以上,再加入适量的石膏进行调节。这类水泥早期强度高、水化热大,适合用于建筑工程中的主体结构施工。
而火山灰水泥则是将部分熟料替换成火山灰质材料,如粉煤灰或火山灰渣。这种水泥的水化反应较慢,但后期强度增长好,且抗侵蚀能力强,常用于水利工程或地下工程。还有矿渣硅酸盐水泥,它用高炉矿渣替代一部分熟料,不仅降低了成本,还能提升耐久性和抗腐蚀性。
我曾经参与过一个项目,需要为一个沿海地区的桥梁选择合适的水泥类型。当时我们对比了多种配方方案,最终选择了掺加大量粉煤灰的火山灰水泥,因为它的抗氯离子渗透能力更强,更适合海洋环境下的长期使用。这让我深刻体会到,水泥的配方不是一成不变的,而是要根据具体应用场景灵活调整。
配方设计的原则与标准
在制定水泥配方时,工程师们并不是随意搭配,而是遵循一系列原则和标准。首先是满足国家标准或行业规范,比如GB 175-2007《通用硅酸盐水泥》就对各类水泥的化学成分、物理性能等做了明确规定。其次要考虑的是原材料的可获得性和经济性,不能一味追求高性能而忽视成本控制。
另外,配方设计还需要兼顾生产工艺的稳定性。例如,某些原料在高温下容易挥发或结块,这就需要在配料阶段做出调整,避免影响后续煅烧过程。同时,还要考虑到水泥的使用环境,比如是否需要早强、缓凝、抗冻或抗渗等功能。
我记得有一次在调试一条新生产线时,发现熟料的易磨性特别差,导致成品细度不达标。后来我们重新调整了原料配比,加入了少量助磨剂,并优化了煅烧温度曲线,问题才得以解决。这说明,一个好的配方不仅要考虑化学反应,还要与整个生产流程紧密结合,才能真正发挥出应有的效果。
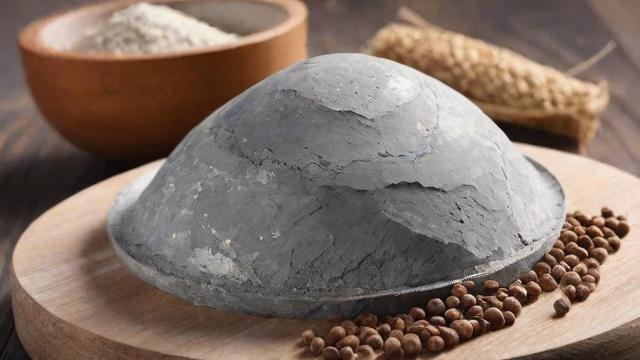
在水泥生产中,光靠基础原材料是远远不够的。为了满足不同工程对水泥性能的多样化需求,工程师们会根据具体情况,在配方中加入各种“调味料”——也就是我们常说的添加剂。这些添加剂虽然添加量不大,但它们的作用却非常关键,能显著改善水泥的工作性、强度发展、凝结时间以及耐久性等。
我第一次接触到添加剂是在一个冬季施工项目里。当时天气特别冷,普通水泥在低温下水化速度变慢,导致混凝土迟迟不凝结,影响了施工进度。后来我们在水泥中加入了早强剂,结果效果非常明显,混凝土很快就开始硬化,大大缩短了拆模时间。这件事让我意识到,添加剂并不是可有可无的“点缀”,而是提升水泥适应性和效率的重要手段。
常见添加剂种类
水泥常用的添加剂种类很多,常见的有缓凝剂、早强剂、减水剂、引气剂、助磨剂和膨胀剂等。每一种都有其特定的功能。比如,缓凝剂主要用于延长水泥浆体的初凝时间,适合高温环境下或需要长时间运输的工程;而早强剂则正好相反,它能加速水泥早期强度的发展,常用于冬季施工或抢工期项目。
减水剂是我工作中用得最多的一种,尤其是在配制高性能混凝土时几乎必不可少。它的作用是减少拌合用水量,同时保持良好的流动性,这样不仅提高了混凝土的密实度,还能增强强度。我记得有一次做泵送混凝土,如果不加高效减水剂,根本无法实现远距离输送,而且容易堵管。
还有些添加剂是为了应对特殊环境而设计的。比如引气剂可以在混凝土内部引入微小气泡,提高抗冻性能;膨胀剂则能补偿混凝土硬化过程中的收缩,防止裂缝产生。这些添加剂看似不起眼,但在关键时刻往往能解决大问题。
添加剂对水泥性能的影响机制
添加剂之所以能改变水泥的性能,是因为它们参与或调控了水泥的水化反应过程。以缓凝剂为例,它通常是一些有机酸或磷酸盐类物质,能够吸附在熟料颗粒表面,形成一层保护膜,延缓水化产物的生成,从而推迟凝结时间。而早强剂多为氯盐或硫酸盐,它们可以促进C3S(硅酸三钙)的水化反应,加快早期强度的增长。
减水剂的作用机制比较复杂,主要是通过静电斥力和空间位阻效应来分散水泥颗粒,使原本聚集在一起的颗粒分散开来,释放出被包裹的自由水。这样一来,就实现了在低水灰比下依然具有良好流动性的混凝土拌合物。
我还记得有一次调试高强混凝土,水胶比已经压得很低,但坍落度还是上不去。后来改用了新一代的聚羧酸系减水剂,配合少量缓凝成分,不仅流动性提上来了,工作性还保持得很好,整个施工过程顺畅了不少。这说明,添加剂之间的协同作用也很重要,合理搭配才能发挥最大效益。
环保型添加剂的发展趋势
随着环保意识的不断增强,传统添加剂中一些可能带来环境负担的成分正逐渐被淘汰。例如,含氯离子的早强剂虽然效果好,但长期使用可能导致钢筋锈蚀,因此现在越来越多地采用硝酸盐或有机胺类替代品。同样,过去常用的木质素磺酸盐减水剂也在被更高效的聚羧酸减水剂取代,后者不仅减水率更高,而且不含对环境有害的成分。
近年来,我也注意到市场上出现了不少基于工业副产品开发的绿色添加剂。比如利用废糖蜜制成的缓凝剂、从粉煤灰中提取的活性组分作为辅助胶凝材料等。这些新型环保添加剂不仅降低了资源浪费,还提升了水泥的整体性能。
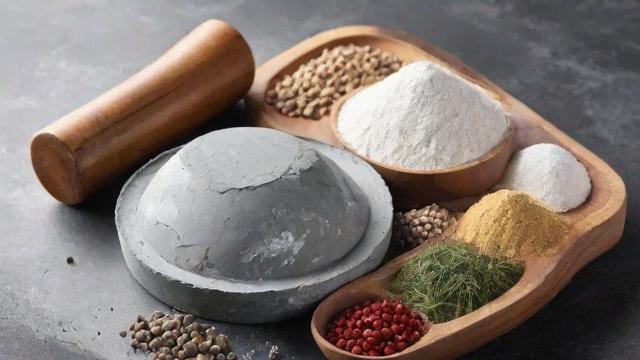
我自己参与过一个绿色建材认证项目,其中一项重要指标就是是否使用了环保型添加剂。最终我们采用了多种新型无氯早强剂和生物基缓凝剂,顺利通过了认证。这个过程中我深刻感受到,未来的水泥配方不仅要考虑性能和成本,更要兼顾可持续发展的要求。
在水泥生产过程中,配方的科学性直接关系到最终产品的性能和质量。但光有好的配方还不够,如何在每一个生产环节中精准执行、动态调整,才是确保水泥品质稳定的关键所在。我曾参与过多个水泥厂的技术支持项目,亲历了从原料配比到成品出厂全过程中的挑战与突破。在这个章节里,我想结合实际经验,分享一下配料阶段的精准控制技术、煅烧过程中配方稳定性的保障措施,以及成品检测与配方优化的策略。
配料阶段的精准控制技术
配料是整个水泥生产流程中最关键的起点之一,它决定了熟料成分的基本结构。在我的理解中,配料就像是做一道复杂的菜,材料的比例必须精确到位,否则味道就会差很多。水泥配料主要依赖石灰石、黏土、铁矿石等原材料,这些材料的化学组成波动较大,因此需要通过在线分析设备实时监测,并借助计算机控制系统进行动态调整。
我在一家水泥厂调试配料系统时,发现由于原料来源不稳定,导致生料成分波动频繁,进而影响了窑系统的热工制度。后来我们引入了X射线荧光分析仪(XRF)配合闭环控制软件,实现了每小时自动修正配料比例的功能。这样一来,即便原料质量出现波动,也能迅速做出反应,确保进入窑内的生料成分始终处于设定范围内。
此外,我还注意到一些先进企业已经开始采用人工智能辅助配料。他们通过历史数据训练模型,预测不同原料组合对熟料质量的影响,从而提前调整配比,避免了大量人工试错的时间成本。这种智能化手段虽然初期投入较高,但从长期来看,不仅提升了产品质量,还显著降低了能耗和原材料浪费。
煅烧过程中配方稳定性的保障措施
当生料粉被送入回转窑后,就开始了高温煅烧过程。这个阶段可以说是水泥熟料形成的“关键时刻”。如果在这个环节中配方控制不当,即使前期配料再精准,也可能前功尽弃。我记得有一次去某工厂巡检,发现他们的窑况波动很大,熟料颜色不一致,强度也忽高忽低。经过排查,问题出在燃烧器调节不当和喂料量不稳定上。
为了保障煅烧过程中配方的稳定性,首先得确保燃料供给均匀、空气配比合理。现在很多水泥厂都配备了先进的燃烧控制系统,可以根据窑内温度、压力和废气成分的变化,自动调整煤粉喷射速度和风量分配。这样不仅有助于维持稳定的煅烧环境,还能提高能源利用效率。
另一个关键点在于窑速和喂料量的匹配。如果喂料太快而窑速跟不上,会导致生料堆积,影响热交换效率;反之则会造成资源浪费。我在一个技改项目中协助客户优化了喂料与窑速联动控制系统,使得物料在窑内的停留时间更加均匀,熟料结粒更致密,整体强度提高了近5MPa。
还有一个不容忽视的因素是火焰形状的控制。火焰太长会冲刷窑皮,缩短窑衬寿命;太短则热量集中,容易造成局部过热。通过更换多通道燃烧器并优化操作参数,我们成功地将熟料f-CaO(游离氧化钙)含量控制在1.0%以下,这对后期水泥强度和安定性都有极大帮助。
成品水泥质量检测与配方优化策略
水泥生产最后一道关口就是成品检测。这一步不仅仅是对产品是否合格的判断,更是为下一轮配方优化提供重要依据。我曾在一个项目中遇到过这样的情况:一批水泥出厂后,在施工方使用过程中出现了凝结时间异常的问题。经过回溯检测,发现问题出在石膏掺量控制不严,导致缓凝效果不佳。
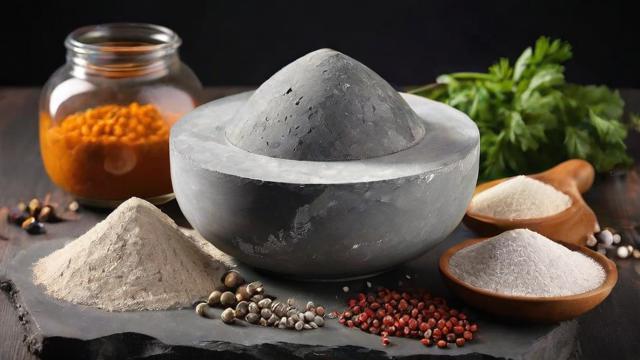
常规的检测项目包括细度、比表面积、凝结时间、安定性和抗压强度等。现在越来越多企业开始引入在线快速检测技术,比如激光粒度分析仪、流动度测定仪和自动压力试验机等,大大提高了检测效率和准确性。同时,我们也建立了完善的数据库系统,把每次检测结果都归档分析,便于追踪趋势变化。
除了被动检测,主动优化也是必不可少的。我们会根据市场反馈和工程需求,定期对现有配方进行评估和微调。例如,针对某地区高温干燥的气候特点,我们在原有基础上增加了少量缓凝剂和保水助剂,使水泥在该区域的适应性显著提升。
更重要的是,我们开始尝试建立“从用户端反推配方”的机制。也就是说,不再只是按照标准来生产,而是充分考虑终端用户的使用场景和性能要求,定制化地调整配方。这种做法虽然对生产管理和质量控制提出了更高要求,但也为我们赢得了更多高端客户的认可。