螺栓拧紧力矩标准与计算方法详解 | 如何正确设置螺栓扭矩值
螺栓拧紧力矩的基本概念与重要性
作为一名经常接触机械设备装配的从业者,我深知螺栓连接在各种工程应用中的重要性。它看似简单,却承载着关键结构的稳定性和安全性。而在这其中,拧紧力矩扮演了至关重要的角色。一个合适的拧紧力矩不仅能确保连接的可靠性,还能避免因过度或不足拧紧带来的潜在风险。接下来的内容,我会从基本原理讲起,带你看清这个“小细节”背后的大学问。
螺栓连接的工作原理
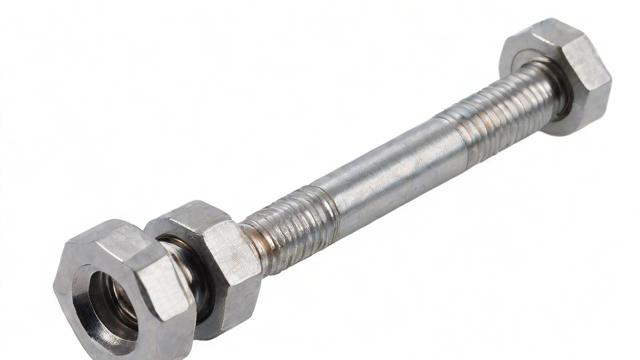
螺栓连接的核心在于通过预紧力将两个或多个部件牢固地结合在一起。当螺栓被拧紧时,螺纹之间的相互作用产生轴向拉力,这种拉力使得连接件之间形成夹紧力,从而防止外部载荷导致的松动或分离。就像我们系鞋带一样,只有绑得足够紧,鞋子才不会在行走中脱落。同样道理,在机械结构中,正确的预紧力是维持连接稳定的基础。如果预紧力不足,连接部位可能会因为振动、热胀冷缩等因素逐渐松脱;而如果预紧力过大,则可能导致螺栓断裂或者连接件变形。
拧紧力矩的定义及其作用
拧紧力矩是指施加在螺栓头部或螺母上,使其旋转并产生预紧力的扭矩值。它直接决定了螺栓连接的初始夹紧力大小。想象一下,如果我们用扳手拧螺丝的时候不控制力度,要么太松容易脱落,要么太紧可能滑丝或者损坏零件。所以,拧紧力矩的作用不仅仅是让螺栓“固定”,更重要的是在安全范围内提供足够的夹紧力,保证连接系统的可靠性和耐久性。特别是在汽车、航空、桥梁等对安全性要求极高的领域,精确控制拧紧力矩几乎是不可妥协的标准操作。
不当拧紧力矩带来的风险
一旦拧紧力矩设置不当,后果可能是灾难性的。最常见的问题就是螺栓松动,尤其是在设备频繁震动或温度变化较大的环境中,轻微的松动会迅速演变为连接失效。另一个极端是拧得过紧,这会导致螺栓承受超过其屈服极限的应力,最终发生断裂。除此之外,在涉及密封结构的应用中,比如发动机缸盖或管道法兰连接,拧紧力矩不均还可能造成密封面变形,进而引发泄漏事故。我曾亲身经历过一次因为力矩未达标而导致的设备故障——一台大型压缩机在运行几小时后突然停机,检查发现是因为部分连接螺栓松动,造成了内部零件错位。那次事件让我深刻意识到,每一个看似微小的参数背后,都隐藏着巨大的责任。
影响拧紧力矩的关键因素
影响拧紧力矩的因素有很多,其中最主要的是材料特性、摩擦系数和螺纹配合情况。不同材质的螺栓(如碳钢、合金钢、不锈钢)具有不同的强度等级,这也直接影响其推荐的最大拧紧力矩值。同时,螺栓与螺母之间的摩擦系数变化极大,例如表面是否润滑、是否有氧化层或涂层都会显著改变实际所需的拧紧力矩。此外,螺纹的加工精度和配合间隙也会影响拧紧过程中的受力分布。这些变量共同作用,使得每一次拧紧操作都需要根据具体情况进行评估和调整。我在工作中就遇到过因为使用了未经润滑的螺栓而导致实际预紧力远低于预期的情况,结果不得不重新拆卸并重新施加正确力矩。这也提醒我们,了解并掌握这些影响因素,是实现精准拧紧的前提。
螺栓拧紧力矩的标准与计算方法
在实际工作中,我常常需要查阅各种标准和参数来确定一个螺栓连接的合适拧紧力矩值。这个过程看似简单,但背后却涉及多个国际规范、材料等级以及复杂的计算公式。掌握这些内容不仅能提高装配效率,还能确保连接的安全性和稳定性。
国际和行业标准概述
为了统一螺栓拧紧力矩的应用规范,全球范围内制定了一系列标准。例如,ISO(国际标准化组织)发布的ISO 898-1标准明确了碳钢和合金钢螺栓的机械性能及对应的拧紧力矩推荐值;ASME(美国机械工程师协会)则针对不同工况下的螺栓连接提供了详细的技术指南;而我国的GB/T系列标准也对各类螺栓的使用条件进行了规定。这些标准并不是互相独立的,很多时候它们之间存在一定的对应关系。比如,在汽车制造领域,通常会参考ISO标准,而在石油化工行业中,则可能更倾向于采用ASME或API的相关规范。我在参与海外项目时就曾遇到过标准不一致的问题,最终通过对照各标准之间的等效性,找到了合适的力矩值。
常见螺栓等级与推荐力矩值
螺栓等级是决定其最大承受力矩的重要依据之一。常见的等级如8.8级、10.9级、12.9级,数字越大表示螺栓强度越高,所能承受的拧紧力矩也就越大。一般来说,每个等级都会对应一张“螺栓拧紧力矩标准表”,里面包含了不同直径(M6、M8、M10等)和不同摩擦系数情况下的推荐力矩值。例如,对于M10的8.8级螺栓,如果摩擦系数为0.14,推荐力矩大约是45Nm左右;而如果是10.9级,则可以提升到约60Nm。这些数据并非一成不变,还会根据润滑状态、表面处理等因素进行调整。我平时在做装配工艺设计时,都会把这些表格打印出来贴在工作台上,方便随时查阅和核对。
拧紧力矩的计算公式及参数说明
虽然有现成的标准表可用,但在某些特殊场合,比如非标螺栓或特殊工况下,我们需要自己进行计算。最常用的公式是:T = K × D × F。其中,T代表所需的拧紧力矩,K是摩擦系数,D是螺栓公称直径,F则是目标预紧力。这个公式看起来简单,但每一项参数的选择都至关重要。尤其是K值,它不仅受螺纹配合的影响,还与是否使用润滑剂密切相关。例如,干摩擦状态下K值可能高达0.2甚至更高,而使用润滑油后可以降低到0.1以下。因此,在计算前必须明确当前的装配条件。有一次我在调试一台进口设备时发现,厂家提供的力矩值明显偏小,后来才意识到他们使用的是低摩擦系数的涂层螺栓,而我们现场用的是普通镀锌件,这提醒我在实际应用中不能照搬照抄,要灵活应对。
预紧力与拧紧角度控制法简介
除了直接控制扭矩外,还有一种更精确的方法叫做“拧紧角度控制法”。这种方法的核心在于先施加一个小的初始扭矩(称为“贴合扭矩”),然后在此基础上继续旋转一定角度,从而实现对预紧力的更精准控制。这种方式特别适用于高强度螺栓或对夹紧力要求极高的连接结构,如发动机缸盖、风电塔筒连接等。因为它能有效避免因摩擦变化导致的预紧力波动。举个例子,某次我们在组装大型液压缸时采用了“扭矩+角度”的双重控制方式,先以30Nm的力矩贴合,再旋转90度完成最终拧紧。这样做的好处是即使现场环境略有差异,也能保证每颗螺栓的预紧力保持一致。这种策略虽然操作复杂一些,但对于关键部位来说,是非常值得投入的。
实际应用中的拧紧策略与质量控制
在日常的装配工作中,我深刻体会到选择合适的拧紧策略对连接质量的重要性。很多时候,光有标准和理论是不够的,必须结合现场条件、工具性能以及工艺要求来制定实际可行的拧紧方案。特别是在一些关键连接部位,比如法兰、发动机缸盖或者大型结构件上,错误的拧紧方法不仅会影响密封性,还可能导致设备故障甚至安全事故。
扭矩控制法与扭矩-转角控制法的比较
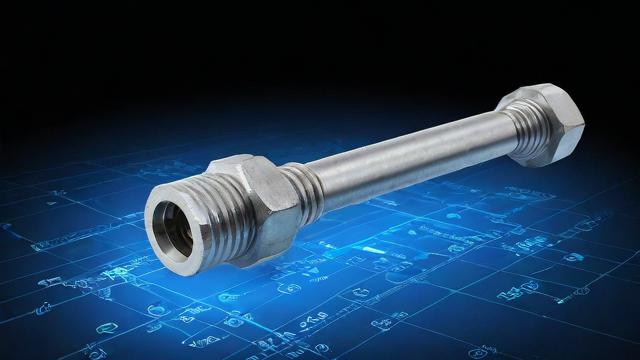
在大多数情况下,我会优先使用扭矩控制法,因为它操作简单、易于执行。只需要设定好目标扭矩值,用扭力扳手或电动工具直接拧紧到指定数值即可。这种方法适用于摩擦系数稳定、工况不太复杂的场合。但我也发现,在高强度螺栓连接中,仅仅依靠扭矩控制往往无法保证预紧力的一致性,因为摩擦系数的变化会直接影响最终夹紧力。这时候,我就会采用扭矩-转角控制法,也就是先施加一个初始扭矩,再以固定角度继续旋转螺栓,使其达到理想预紧状态。这种做法虽然多了一道工序,但在关键连接中能显著提升一致性,比如我们在组装液压系统高压管路法兰时就采用了这种方式,结果密封效果明显改善。
拧紧工具的选择与校准
拧紧工具的精度和稳定性直接决定了最终连接的质量。在我参与的多个项目中,都会根据不同的应用场景选择不同类型的拧紧工具。对于小型维修或低强度装配,手动扭力扳手是最常用的选择,它操作灵活且成本低,但依赖人工经验,容易出现误差。而在生产线或高精度要求的场合,我们会选用气动扳手或电动拧紧机,这些工具可以精确设定扭矩值,并具备数据记录功能,便于后期追溯。例如,有一次我们为一家汽车零部件厂设计装配线,就选用了带反馈系统的电动拧紧枪,每次拧紧完成后都会自动生成报告,确保每颗螺栓都符合标准。此外,无论使用哪种工具,定期校准都是不可忽视的环节。我们通常每月送检一次,确保工具的精度误差控制在±3%以内,这样才不会影响整体装配质量。
多步拧紧工艺的应用场景
在处理法兰连接这类需要均匀受力的结构时,我发现单次拧紧很难做到各点受力一致,容易导致密封不严或局部应力集中。因此,我通常会采用“多步拧紧”工艺,也就是将整个拧紧过程分为几个阶段逐步完成。例如,第一步先以较低的扭矩值(如最终值的50%)按顺序初步拧紧所有螺栓;第二步再提升至75%的扭矩进行二次拧紧;最后一步才完全拧紧到目标值。这样做可以让法兰面均匀贴合,避免因局部过紧而造成变形。我们曾经在一个天然气管道项目中严格按照三步法执行,结果安装后的泄漏率几乎为零,客户对此非常满意。这种分阶段拧紧的方法虽然耗时稍长,但对于重要连接来说是非常值得投入的。
质量检测与拧紧过程监控技术
拧紧完成后,并不意味着工作就结束了。我始终坚持“拧得准不如测得准”的原则,所以在很多关键连接中都会安排质量检测环节。最常用的是扭矩测试仪,它可以回测已经拧紧的螺栓是否达到了设定值。不过这种方法存在一定的局限性,比如不能准确反映真实预紧力。因此,我们也开始引入超声波测量技术,通过检测螺栓伸长量来反推预紧力大小,这种方法更加精准,尤其适合高强度螺栓的检测。记得在一次风电塔筒维护任务中,我们就利用超声波检测发现了几颗预紧力不足的螺栓,及时进行了补拧,避免了潜在的安全隐患。除此之外,现在很多自动化装配线上还会配备在线监控系统,实时采集每颗螺栓的拧紧曲线,并自动判断是否合格,大大提升了装配质量和可追溯性。